- Removing dust and debris with compressed air or clean, lint-free cloths
- Sand down and clean loose paint or flaking surfaces
- Wash off dirt with a mild detergent and allow to dry completely, including drywall and painted surfaces
- Thoroughly rinse detergents to remove any residual residue
- Clean off greasy, oily and waxy areas of any surface, but use clean rags frequently. This avoids unnecessary spreading of the contaminants
- Using firm, even pressure during application. Laminating rollers can help chase out air bubbles and press the adhesive into crevices and bumps. Let the type of substrate dictate the amount of pressure used. For example, gator board needs less pressure than a textured wall.
- Warming the material helps soften the adhesive enough to let it easily flow into any textured surfaces. This is particularly useful with acrylic-based adhesives. It’s important not to overheat the magnet, as it will damage the rubber binding and can demagnetize the material if the temperatures are too hot.
- Supplementing any gaps or uneven surface areas with foam tape or additional adhesive. Remember, the overall goal is to keep the entire substrate in contact with PSA.
FEATURED POST
Make it Stick with Magnetic Sheeting
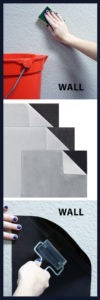
Make it Stick with Magnetic Sheeting
By Shalea Hardison
Using magnetic sheeting or magnetic strip with pre-applied Pressure Sensitive Adhesives (PSAs) brings significant benefits to your project. Incorporating surface preparation, adhesive selection and good installation techniques provide the best results for PSAs.
Technically applied as a laminate in the factory, PSAs provide a superior bond between the magnetic material and the adhesive. However, in order to achieve the best possible adhesion between the PSA and the substrate, set yourself up for success by following these best practices.
Good surface preparation, adhesive selection and strong installation techniques take the stress out of using pressure sensitive adhesives with magnetic sheeting.
Surface Prep
Providing a clean surface is a crucial first step in achieving quality adhesion with your PSA. Problems with adhesion are frequently traced back to the failure to properly prepare the substrate first. Always clean the substrate, as PSAs adhere best when the surface is free from contaminates and imperfections. Accomplish great surface prep by:
Adhesive Selection
Selecting the best type of adhesive for the application largely influences the success of the PSA. A project used outside in July requires a different adhesive than one used indoors for a sign application. We supply flexible magnetic material with three types of adhesive: rubber-based, acrylic-based and free film.
In general, rubber-based adhesives, with their flexible and viscous nature, bond very well to a variety of surfaces. But they have temperature and UV limitations, as well as some chemical surface interactions. Acrylic-based adhesives typically adhere well to vinyl, metal and some plastics. They have excellent temperature resistance and durability, however their stiff, low-flow characteristics require experience and best practices to optimize adhesion. Free film adhesive, with a single bond of adhesive, is a low-cost alternative for applications such as craft and hobby. It is best suited to light-weight paper substrates.
We also recommend testing a small sample of the material on the prepared substrate to best determine compatibility and see if any other preparation was overlooked.
Master Magnetics’ Flexible Magnetic Materials with PSA
Surface Contact
In order to achieve a quality bond, it is important for the substrate to have as much direct contact as possible with the PSA. The pressure sensitive adhesives with magnetic sheeting comes pre-applied. The benefit to this is that the adhesive is bonded or laminated to the magnet. So the focus turns to achieving the optimal bond with the substrate. This can best be achieved three ways:
Cure Times
Always allow the magnetic material to fully cure prior to use. Acrylic-based adhesives, including free film adhesives, need a minimum of 24 hours to cure – longer in extremely humid or warm environments. Rubber-based adhesives bond immediately, but will reach even greater potential after 24 hours. This final step directly impacts the success or failure of the PSA.
These few simple guidelines for utilizing pressure sensitive adhesives with magnetic sheeting helps result in quality bonds with the substrates. Typically, our flexible magnetic material with PSA, has the adhesive applied to the magnet’s weak side. Double magnetized, double laminated, custom cutting and slitting is also available.
Our knowledgeable sales team can assist you with the selection of the right magnet material and adhesive for your project. Contact us with questions and samples.